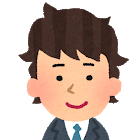
『不具合品の流出に対しての「要因分析」を提出しろ!』
って、言われたんですが「要因分析」って何?どうしたらいいの?
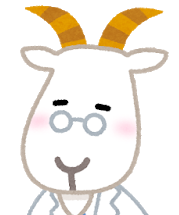
はい!それでは今回は「要因分析」の手法として有名な
“なぜなぜ分析”(5 Whys)について勉強していきましょう!
あるべき姿と現状のギャップが問題です。あるべき姿へと改善するためには、”なぜ?そのような問題が起きたのか?”が、分からなければ対策もできません。そのため、その問題が発生した要因を見付けるための分析が要因分析です。その要因分析を行う手法として、なぜなぜ分析があります。
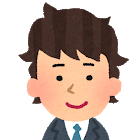
これまでの先輩たちの対策書を見て参考にしようとしたら
だいたい、要因分析結果の欄が同じなんですけど…
じゃ、僕も先輩と同じこと書いておけばいいか!
こういうこと、多くないですか?
「いつも同じ内容の要因分析になってしまっている。」これは、要因を特定して問題解決が出来ていないために問題が再発している状態。または、そもそも要因分析もしていないので、対応策にもなっていない状態です。
たしかに要因を特定して問題を解決していくことは、とても時間もかかりますし大変です。
しかし、要因対策ができておらず、問題再発を繰り返しているとどうなると思いますか?
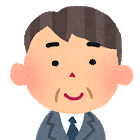
主任さんって、いつも同じミスするな…
もう少し注意深く見ておかないと危ないな…
このように上司やお客さん、同僚の不信感が増し、より自分に向けられる注意が厳しくなります。
そうなると、チェックが厳しくなりますから品質要求も高くなり、ちょっとしたことでも指摘を受けるようになってしまいます。
結果として対応に追われて忙しく、ますます十分な対処ができずに問題の火種が大きくなってしまいます。それでも同じ対応を続ければ、当然手が打てないほど状況が悪化することになります。
“なぜなぜ分析”とは
トヨタ生産方式の”なぜなぜ分析”では、工場現場にある生産機械が故障して止まった時の「なぜ機械は止まったのか?」を例に著書でも紹介されており、特に生産現場に有効な手段であると言えます。
では、具体的に”なぜなぜ分析”とはどういったものなのか簡単に説明します。
生産機械が止まってしまい、生産が遅れてしまいました。
これについて要因分析して対策書を出すこととなった主任さん。
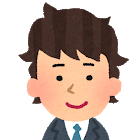
要因は、オーバーロードがかかってヒューズが切れたため。
対策は、ヒューズの交換!
これでよし!仕事も忙しいし、パパっと対策しないとね。
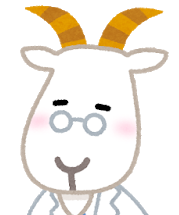
はい。これでは、要因対策ではなくただの不具合処置ですね。
ヒューズを交換して機械を動かしたら、またヒューズが切れてしまう。
こういったように再発を繰り返してしまうことにつながります。
今回は簡単な事例で小芝居してもらいましたが、この事例はトヨタ生産方式の中で紹介されている事例をそのまま持ってきてみました。
このように、ただの不具合処置となってしまうと、すぐにまたオーバーロードがかかる状況となりヒューズが切れて、機械が止まってしまいます。オーバーロードがかかる要因を特定していくことがとても大切です。
①オーバーロードがかかって、ヒューズが切れた
↓
②軸受部の潤滑が十分でなかった
↓
③潤滑ポンプが十分汲み上げていなかった
↓
④ポンプの軸が摩耗していた
↓
⑤濾過機が付いていないため、切子が潤滑油に入っていた
大野耐一氏の著書『トヨタ生産方式』(ダイヤモンド社) より
具体的には、このように5回のなぜを繰り返すことで、「では、濾過機を取り付けて切子が入り込まないように対策を取ろう!」と、真因である切子が入ってポンプの軸を痛めていたことからオーバーロードがかかった問題の解決に向けて対策を取ることができるのです。
これがトヨタ生産方式における「なぜなぜ分析」の考え方の基本となります。
“なぜなぜ分析”のやり方
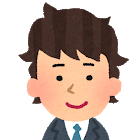
品管さんにも、なぜなぜを5回繰り返せと言われたんですけど、
5回もできなかったり、6回でも7回でも出来そうなときもありますよ。
ネットで調べると5回はただの参考だーってのもありました。
いったい何が正しいんでしょう???
このように、なぜなぜを5回繰り返す事例や、2回でも3回でも大丈夫としている事例もあります。なぜこのように色々と多くのやり方があるのでしょう?
トヨタ自動車で”なぜなぜ分析”を学んだという方々でも、5回繰り返すと言う人もいれば、2回でも3回でも大丈夫と言う人もいます。主任さんが言うように、ネットや書籍、セミナーなどでもやり方はそれぞれ違います。
色々と話を聞いてみると、実は基本的に細かくルール化されているわけではないようです。
ガチガチに手法を固めると柔軟性がなく、結局型にはまった問題しか解決できなくなります。だから、最初は基本的には”5回なぜなぜ繰り返す”ということで学ぶのですが、それはあくまでも基本の型です。そこから徐々に部署やグループ、個人にそれぞれ合ったやり方へと変わっていくために、色々なやり方が生まれたと言えそうです。
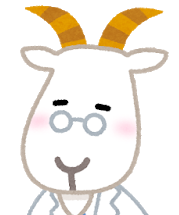
ようするに、どの手法も正しいやり方です。
「守破離」で考えてみましょう。「守」の段階の教材では5回のなぜなぜを基本として教えますが、「離」まで昇華させた熟練者たちが自身の手法として教えるものは独特の個性があります。
ですから、様々な習得段階の人たちのやり方があふれているのだと思います。
それぞれの業務環境では、そのやり方が正しく、実績もあり、一つの型となったものです。
そのため、様々なやり方を試してみて、しっくりくるもので取り組む。それで良く、それを基本にまた自分自身の型を作っていくことが一番。何事も訓練ですね。
“なぜなぜ分析”をする上での考え方
幹となる部分
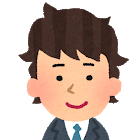
とりあえずやってみる感じですか…?
そもそもの基本も知らないので、どうしたら良いか…?
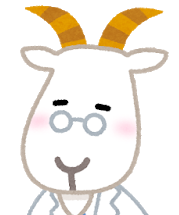
では、まず様々なやり方に共通した幹となる部分、5つの基本。
ここさえ押さえれば大きな間違いなく要因分析は進められますよ。
1つ目:「なぜ」を5回繰り返すことにこだわらない
一番間違いの多い部分です。
「5 Whys」と英訳されてしまっていることもあり、5回繰り返すことが正しいと思うという人がとても多いです。帳票自体が5回分が空欄になっていて、その空欄を埋めて検討するように指示されるものを使用しているところもあるでしょう。
ですが、問題として認識した箇所が異なれば5回が3回になることも、7回になることもあります。ですから、5回という回数にはこだわらず、真因に辿り着いたところで止めることが大事です。
例えば、トヨタ生産方式の説明は基本の5回にまとめるために具体的な事象は省いたのかなと思っています。具体的な事象を加えると、
①オーバーロードがかかって、ヒューズが切れた
↓ この間に「摩擦力が高くなった」
②軸受部の潤滑が十分でなかった
2つ目:「なぜならば~」で問いかけ
さきほどのトヨタ生産方式に出てきた事例で説明します。
①オーバーロードがかかって、ヒューズが切れた
↓ (なぜならば)
②軸受部の潤滑が十分でなかった(から)
このようにひとつ要因をより下げるときに使うのが、この「なぜならば~だから」です。この「なぜならば」を入れたことで文章がつながらない、違和感を感じる場合にはその要因は正しくないのです。
3つ目:「~なので」で確認の問いかけ
次は要因から問題につながるかを確認します。
②軸受部の潤滑が十分でなかった
↓ (ので)
①オーバーロードがかかって、ヒューズが切れた
つながりますね。逆から読んだときに「なんか話が飛躍してる?」と感じた場合は注意が必要です。経験に基づく想像や、対策ありきで要因を書いた場合に多く見付かります。
4つ目:三現則で事実を見る
経験者になるほどこれが守れず、いつまで経っても処置で終わってしまう人が多いです。
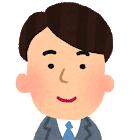
またこの故障か。この時はここが悪いから、ここを直せばOK。
はい、対応完了。要因はこれこれっと。
こんな感じで、過去の経験で対処の仕方を知っていると、調べないで要因をこれだと思い込んでしまうことが増えます。そして、その対処に合うようになぜなぜ分析をまとめていってしまいます。
要因分析をきちんと行うためには、現地・現物・現実に則り、問題が発生した場所で、実際の問題が発生しているものを確認し、現実をしっかりと見て分析することが重要になります。
特に、また同じ故障が起きたのであれば、前回の対策は要因対策ではなく処置であった可能性が高いので、改めて現地・現物・現実での確認が必要と言えます。
5つ目:掘り下げるのは自身で解決できるところまで
最後のポイントは、どこまで掘り下げれば真因に辿り着いたと言えるのか?です。
「自分は悪くない」、「怒られたくない」といった思いが強いときによく見られるのが、「お客さんの指示が悪い」、「上司が悪い」、「社会が悪い」というものです。
結局これをしてしまうと、この後の対策が立てられなくなってしまいます。なぜなぜ分析を行う目的は、要因を分析して対策をすることです。対策が取れないようなことを要因としてしまうことは意味がないのです。
確かに、お客さんの指示が悪かったり、上司が悪かったり、社会情勢の影響もあるかもしれません。ですが、なぜなぜ分析をする上では、あくまでも自身の手に負える範囲で問題点を掘り下げることを意識すると整理がしやすくなりますよ。
まとめ
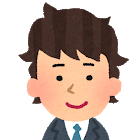
1つ目:「なぜ」を5回繰り返すことにこだわらない
2つ目:「なぜならば~」で問いかけ
3つ目:「~なので」で確認の問いかけ
4つ目:三現則で事実を見る
5つ目:掘り下げるのは自身で解決できるところまで
ですね!
これらの内容も実際に取り組んでみると、難しいと感じられる内容だと思います。ですが、身に着けるためには繰り返しトレーニングするしかありません。
最初は時間も掛かりますが、根気よく取り組んでいくことで、各段に再発防止につながる改善が行うことができます。結果として、負担軽減や生産性効率化、費用の削減、会社の信用につながる活動となりますので、がんばってください。