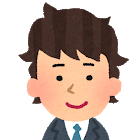
あぁ、また量産開始直前に設計変更。
いつもバタバタで量産開始になって、量産でも不具合が多発。
なんとかなりませんか?
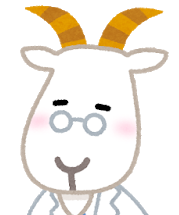
後工程になって設計のやり直しは、致命的な影響が出ますよね。
ところで、FMEAはちゃんとやられてますか?
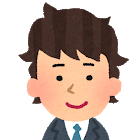
まぁ、ちゃんととは言いませんけど。
ルール上、図面発行前にFMEAの書類出すことになってますし。
いつも前にやったものを確認しながらのコピペが多いですけど、
設計担当者がやってますね。
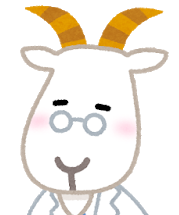
もしかしたら、やり方がまずいかもしれませんね。
FMEAは設計者だけで行うものではありません。
変化点を掴んで、顧客要求に合わせてみんなで事前に
検討することで後工程での改修やムダも省けますよ。
FMEAとは、Failure Mode and Effects Analysis(故障モード影響解析)の頭文字を取った言葉です。要するに、製品や製造プロセスにおけるリスクを設計段階で評価して、取り除く方法を検討する手法になります。事前に問題点を抽出し、対策を検討しておくことで被害の防止や後から行うムダな対処が必要なくなります。
製品設計段階で行うFMEAを設計FMEA、製造プロセスの設計段階で行うFMEAを工程FMEAと呼んだりもしますね。
非常に難しいFMEAですが、設計担当者だけで行うものではなく、プロジェクトチームみんなで行うことで効果が十分に発揮されます。
と、いうことをまずは頭に入れていただくとともに、この難しいFMEAを行うにあたって参画する関係部門のメンバーもFMEAってどんなものかを理解しておくことが重要になります。目的も知らずに参画しても十分な活動にならないばかりか、時間のムダにもなりますからね。
と、いうことで、今回はこのFMEAとはどんなものなのか、簡単に整理していきます。
FMEAとは
FMEAとは、次の3点を行うための系統的な解析ツールです。
- 製品・プロセスの潜在的故障と、その影響を認識し、評価する。
- 潜在的故障の発生の機会を解消または減少させ得る処置の明確化を行う。
- これら全プロセスの文書化を行う。
「潜在的故障」と書くと難しく感じますが、要はこの製品やプロセスの中に本来の機能や性能を落とすような不具合につながる問題点がないかを探し、その問題点を取り除くための方法を見つけようというものです。
【参考】 他のツールとの違いは?
よくある故障に対する解析手法では、「FTA(Fault Tree Analysis)」や「DRBFM(Design Review Based on Failure Mode)」などがあります。
FTA:発生した問題や故障を起点として要因分析をしていくトップダウン解析の手法です。FMEAでは製品やプロセスから発生しそうな問題や故障を推測しながら行う、ボトムアップ解析であり、考える方向が異なります。
DRBFM:FMEAは、とても難しい手法です。時間がかかったり、使いこなせない人も多かったりします。そこで、より分かりやすく、使いやすいツールとしてトヨタ自動車が開発した手法がDRBFMです。使いやすくするために、顧客への影響度のみで重要度を評価するなど、分析する範囲を狭めていることが特徴です。また、Designとあるように製品設計でしか使えないですし、全く新しい製品設計をする場合には使えないなどの制約もあります。
FMEAの目的は?
FMEAを行う目的は、
- 設計改善・工程改善(継続的な改善の実施)
- リスクの高い故障モードの発生防止
- 習得した教訓(過去トラ)の蓄積と活用
- 特殊特性、重点管理特性、管理項目などの決定
- コントロールプランへの展開
などがあります。
発生しそうな問題や故障の優先順位を設け、重要なものから順に対処することで開発期間を有効に使うことができます。場合によっては、”厳しさ × 発生頻度 × 検出難易度”の点数が、何点以下の問題や故障には処置を行わないというルールを設ける場合もあります。しかし、これについては賛否両論ありますので、FMEAを行うチーム内で認識を事前に合わせておくと、後々のトラブルに発展することを防ぐことができると思います。
私は、点数が低くてもすぐに対処できるものであれば対処することを推奨しています。
いずれにせよ、FMEAを行うことで、問題や故障の優先順位が明確になることで、今後の活動における優先順位も明確になります。これにより、活動がシステマティックに行えるので生産性の向上が期待できますね。
FMEAを実施するタイミングは?
FMEAを実施するタイミングは、
設計FMEA
構想設計前に開始し、設計リリース(最終の図面発行や仕様書発行等)の前には完了します。
工程FMEA
フィージビリティスタディや生産用治工具などの製作前に開始し、量産開始前には完了します。
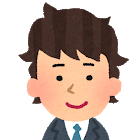
あれ?
量産開始前までに完了?
かなり完了時期が遅くないですか?
このFMEAという手法は、一回集まって解析したら終わりというものではないためです。
例えば、工程FMEAを例にしてみますと、「みんなで集まって解析」→「問題に対する対処方法を抽出」→「推奨措置を決める」→「実際にやってみる」→「効果が認められたか評価する」→「完了」、というような流れで進められます。
また、量産している製品で不具合があった場合には、その内容も反映させていく必要が出てきます。
要するに、量産開始までは常に更新を繰り返し、最善の工程を作っていくことが求められていますので、この時期の完了となっています。
こういった帳票のことを「リビングドキュメント(Living Document)」とも言ったりしますが、常に更新がされ最新版管理していくことで、解析が玉成され、自然と素晴らしい工程が出来上がっていきます。
FMEAを実施する上でのポイントは?
FMEAは、先にも書いたようにとても難しい手法です。そのため、設計担当者などは実施する上での細かなやり方や作法みたいなものを上司がOJTなどを通じて教育しながら進めるのが望ましいです。
しかし、私の経験上やり方は十人十色です。会社間の違いはもちろんのこと、同じ社内でも人によって差がありますので、一部Off-JTも取り入れて外部講習などと併用することも有効になってくると思います。
少し話がそれましたが、今回は設計担当者ではない人向けの記事となりますので、主管する設計担当者によるやり方は別の教育やサイトにお任せして、一緒に参画すべき関係者にフォーカスしたポイントを整理します。
CFTメンバーで実施する
冒頭のストーリーのように、あなたの会社では、設計担当者が一人でFMEAを行っていませんか?
もし、Yesであるなら、その設計者は一人で「製品やプロセスにおける潜在的故障の要因や、故障時の影響範囲」を分析できるだけの力量を有しているでしょうか?
設計担当者以外の品質管理面、物流面、費用面、製造面などの様々な技術や知識、経験がなければ、どのような故障が発生し、それが顧客や自社、仕入先にどういった影響を及ぼすかといったことまで解析できませんよね。
FMEAでは、まだ発生していない問題や故障を予測して解析しますから、様々な関係部署が集まって、それぞれの専門的な視点で問題や故障を抽出することが大切です。
また、対処においても設計者が考えた対処を取ったことで後工程で別の問題につながることもあります。そういったところを互いの情報を共有し、より良い対処方法を決めていくことが大切です。
前工程、後工程の流れを意識する
設計FMEAを行うには、「機能ブロック図」「顧客要求(性能や機能)」「過去トラ」などの情報が必要です。工程FMEAでは、「設計FMEA」「工程フロー図」「工程管理等の情報」などが必要です。
そして、「工程FMEA」を使って「コントロールプラン」を作成し、「作業指示書」や「標準作業書」、「始業前点検表」などの製造管理していくための書類へとつながっていきます。
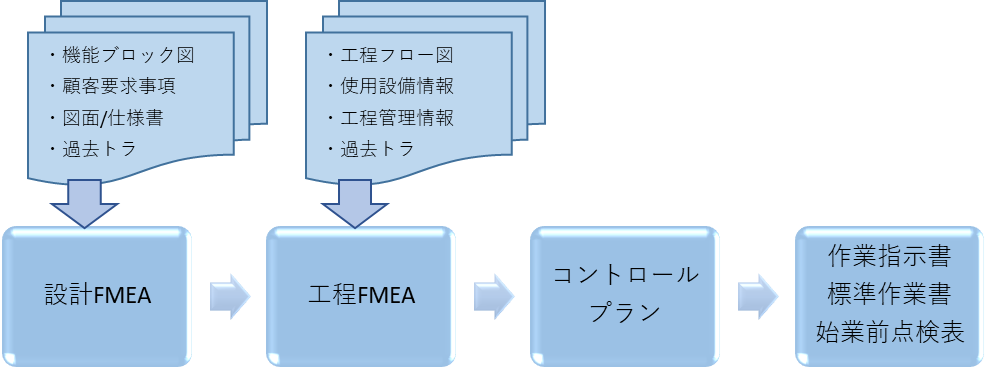
そのため、工程FMEAを意識していない設計FMEAでは、工程FMEAを作成する際に抜け漏れが発生することにもつながり、十分な分析ができないことにもなりかねません。
そして、最終的には製造現場の指示書などの不備にもつながりますので、不具合品の発生や流出にもつながるリスクが出ます。ただやるだけにならないよう、上流の活動ほど後工程のこと、製造のことを考えた活動をすることが大切です。
このことからも、後工程である関係部門の担当者が参画していると、必要な解析項目が分かりやすく共有できることで重要なポイントが抑えられることが分かるのではないでしょうか。
処置を検討する上での留意点
- リスク低減処置を検討する際の優先順位に注意しましょう。
”厳しさ=被害の大きさ”です。厳しさを下げる処置を取らずに発生頻度を下げる処置を取ったとしても、発生が0にならなければ、人命にかかわるような重大な事故につながる危険性が残ってしまう可能性もあります。
故障が発生しても重大な被害につながらないようにすることが第1優先の処置とすべきです。
発生頻度を下げる前に検出難易度を下げた場合も同様です。大量に発生したものを流出しないように検査員がチェックするというのは、チェック漏れが発生した場合には流出につながってしまいます。根本原因となる問題を発生させないような対処を優先的に行う方が、効果的な処置といえます。

- 厳しさ、発生頻度、検出難易度の高い項目がなくても、改善すべき項目をチームで選定して処置を検討しましょう。
先ほども書きましたが、費用対効果を意識してチームで考えるべきです。
発生頻度が100万件に1件で、トラブル発生時の損害が数万円程度の問題に対して、数百万円もかかる、数カ月も要するような対策を取ることはムダが多いです。そのあたりの判断基準をチーム内で相談して決めていけると良いと思います。 - FMEAで厳しさを低減するための処置を取る場合、設計変更を伴うことを理解しましょう。
例えば、センサーによる自動診断機能を付ける(ダイアグノーシス機能の追加)や、一部の機能が停止しても全体が止まらないようにする(冗長設計)、異常発生した場合でも安全側に動作する設定の追加(フェールセーフ機能)といった処置です。これらを行うには設計変更を行い、機能を付与する必要があります。
設計してしまってからFMEAを行うと、後で改修が発生するなどのムダな時間と費用が発生してしまいますので、設計リリース前にFMEAを行うことが重要です。 - 故障の発生頻度を低減する処置は、設計変更、工程変更あるいは設計プロセスの改善を伴うことを理解しましょう。
例えば、バラツキや誤差を考慮した公差を持たせた設計をする(安全強度設計)、人がミスしようとしてもできないようにする工夫(ポカヨケ、フールプルーフ)、事前検証やデザインレビューの行い方の見直しなど。こちらも同様に設計する前にFMEAをやるべき根拠になっています。
まとめ
FMEAとは、
製品やプロセスの潜在的故障とその影響を認識し、評価することで、その故障の発生機会を解消または減少させるための処置を明確化すること。そして、それら全プロセスを文書化し、自社のノウハウとしていくことができるツールです。
そして、蓄積したノウハウは過去トラなどのように、知識や経験として継続的な改善につなげることで、競争力の優位性を保有することにもなります。
プロジェクトの推進における事前の検証をCFTメンバーで行うことで、多面的な視点で問題抽出ができ、後工程でのトライブルを未然に防ぐことができるツールです。
顧客や仕入先、後工程におけるトラブルを防ぐとともに、後工程における時間や費用のムダを削減することにもつながり、より生産性の高い活動が行えるようになります。
と、いうことで、FMEAを設計担当者任せにしていると、量産開始直前になっても設計変更が必要となったり、設備や治工具の改修が終わらずに生産体制が整わないなどの問題が発生しやすくなります。何事も前工程で不十分な活動があると、後工程に行くほど大変になります。
FMEAの目的を理解し、関係者がチームとして一緒にFMEAが行えるような組織が構築できると、生産性は向上し、競争力のある強い会社になっていきますよ。